Blog
How difficult is it for the United States to re industrialize?
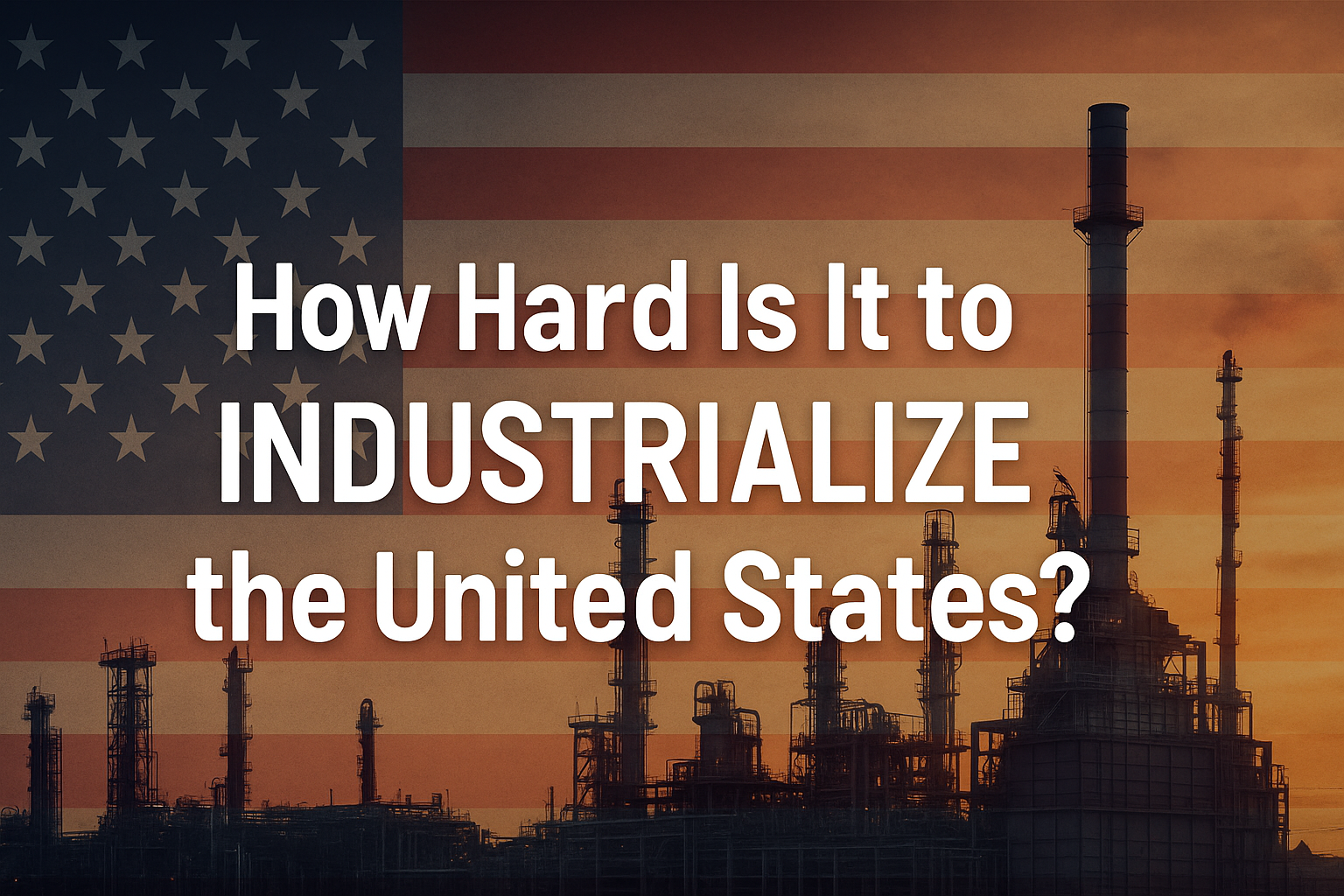
The idea of a U.S. manufacturing revival is gaining traction across political, economic, and national security conversations. But while the intention to re-industrialize the United States sounds simple on paper, the reality is a maze of economic, logistical, cultural, and policy-related hurdles.
So, how difficult is it really for the U.S. to re-industrialize? The short answer: extremely. Let’s break it down.
1. Capital
2. Management
3. Supply Chain
4. Equipment
5. Others
1. Capital
To industrialize effectively, a nation must commit long-term capital at a scale that supports not only factories but entire industrial ecosystems. People who have never managed a company or run a factory may not realize the importance of cash flow. A factory can survive with low profits—or even operate at a loss for a while—but it must have cash flow.
1.1 The average net profit margin for factories nowadays is about 5–8%. To invest in an overseas factory with a reasonable scale typically requires about 20 million RMB (this refers to the situation in Vietnam; our investments in the U.S. are in the hundreds of millions). How many factories have 20 million RMB in idle cash sitting in the bank?
1.2 Even if the factory can come up with 20 million RMB upfront, how will it cover subsequent working capital? Overseas factories usually lose money for 3–4 years before solving problems related to supply chains, production ramp-up, and management. Just the working capital during these years will likely be in the tens of millions, meaning continued financial support from the domestic side is needed.
1.3 Another very tricky issue: how to move the money out of China?
If you haven’t done foreign trade before, you likely don’t have any foreign currency on hand. Exchanging RMB through the bank is almost impossible. Don’t even think about applying for official overseas investment approvals from the government—those quotas are reserved for publicly listed companies.
Underground banks? You’ll be “invited for tea.”
If you have done foreign trade before, you may have U.S. dollars—but those are tied to tax rebates back in China. You can forgo the rebate and transfer money from Hong Kong or overseas accounts, but doing so will cost you 10% of the tax rebate. These are all invisible barriers.
To re-industrialize the United States, federal and state-level policies must align to reduce risk and incentivize long-term industrial investment.
2. Management
The biggest challenge is management. Anyone who’s worked in manufacturing knows how critical the factory director or plant manager is to success. A good manager can significantly impact production efficiency, yield rate, and material usage. To industrialize, you need people—skilled workers, engineers, plant managers, and technicians. Unfortunately, the U.S. is facing a major industrial labor shortage. Why can some factories make higher profits even when making the same products? It’s all about squeezing efficiencies out of the details.
Our factory specializes in injection molding products, currently focused on just two products and three SKUs. We entered the market in 2016 and only began production in 2020. Soon after launching, COVID-19 hit, and we had to invest a lot again just to restart operations. After several years of operation, we found that management talent was the hardest part.
Let’s not even talk about the unique challenges Chinese companies face when manufacturing in the U.S.—even for any company, setting up a factory in the U.S. is incredibly difficult. The U.S. gave up on manufacturing long ago, and the issue isn’t just the decay of infrastructure—there’s a talent gap.
We used to send staff from China, whoever had a visa went. But this is not sustainable:
-
Regular visas don’t allow long stays.
-
By the time a manager becomes familiar with the operations, they have to return.
-
There’s no one to take over.
-
Some overstayed and ended up blacklisted, stopped at customs and held for questioning.
We spent a long time just to find one plant manager with previous experience (from a BMW factory), but even then, his capability and sense of responsibility don’t compare to what we find in China.
Now we’re trying to use the L1 visa, but even that is not going smoothly.
3. Supply Chain
Manufacturing is the culmination of a complete supply chain. Missing a roll of tape or a single screw can delay shipments.
Many BOM components are 10 to 30 times more expensive than in China. For example, getting a quote for just cardboard boxes takes forever. Box manufacturers take a long time to respond, and communication is often difficult. In China, this might take just a single day. This is just the tip of the iceberg when it comes to supply chain challenges.
Logistics is another major pain point:
-
Extremely high costs
-
Difficult to find transport companies
During the pandemic, Walmart was offering $300,000–400,000 annual salaries to drivers, and still couldn’t hire enough.
However, some production inputs are cheaper than in China:
-
For example, PP materials, and
-
Electricity costs (the more you use, the cheaper it gets, which is the opposite of China)
To industrialize successfully, the U.S. must rebuild localized supply chains in key industries like electronics, automotive, and medical devices.
4. Equipment
We are just a simple injection molding factory. All our injection machines and molds were prepared in China and shipped overseas—a sort of reverse OEM model. In China, engineers and electricians are on standby 24/7.
In the U.S., forget it. Luckily, Haitian (injection molding machine manufacturer) has a presence in the U.S.
-
They come in for major problems.
-
I handle minor issues myself.
We can’t afford American-made injection molding machines.
Fortunately, Chinese machines are of excellent quality.
Other automation equipment, such as packaging and conveyor systems, were tested in China and then shipped over.
5. Others
At one point, we wanted to expand capacity and build new facilities. This required government approval and hiring a construction company. But the construction company could only start a year later, and their pricing was astronomical. We had no choice but to negotiate with the government to bring modular prefab wall panels from China. The government said no, citing quality control concerns. We had to find another construction company and pay a huge price.
Can the U.S. Industrialize Again?
Yes, but not without structural transformation.
To industrialize, the United States must:
-
Rebuild vocational training and industrial education
-
Develop regional supply chain clusters
-
Simplify industrial regulations
-
Offer long-term incentives for advanced manufacturing
-
Restore national pride in building things
Conclusion: Industrialize the Right Way—With Strategy and Commitment
The desire to industrialize the United States isn’t just about restoring jobs—it’s about securing economic independence, technological leadership, and national security.
But slogans won’t be enough. The U.S. must commit to:
-
Deep investment
-
Strategic planning
-
Cultural realignment
Only then can we truly industrialize in a way that’s sustainable, scalable, and globally competitive.