Blog
How to implement small batch customized product design?
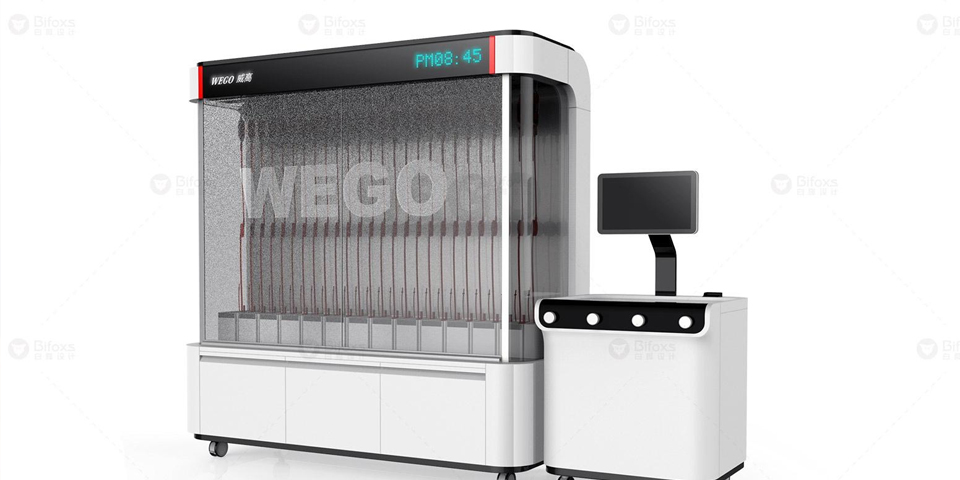
Products come in many varieties. For those with high demand and large projected production volumes, it’s easy to secure molds, production capacity, and various supply chain resources.
However, there are also products with naturally low demand — only requiring a few dozen to a hundred units, such as medical devices or robots. These products typically don’t have large-scale needs, making the high cost and long lead time of steel molds a real challenge.
So, how do we solve this dilemma? The key is to pay special attention to certain factors during the design phase for low-volume products. Take, for example, this medical product — a filtration cabinet. It is a customized item with limited demand, high tooling costs, and a long development cycle.
When dealing with such challenging product designs, we can consider the following strategies to bring the product to life:
-
Process Selection: Injection molding always requires tooling. For small-batch products, using large injection-molded parts is generally not suitable because the mold cost, when spread across a small quantity, makes each unit very expensive. Unless the product offers extremely high added value (like cutting-edge technology), such costs are hard to justify.
-
If plastic parts are necessary due to functional or aesthetic reasons, we can optimize the structure to reduce the mechanical stress on these parts and manufacture them using 3D printing, CNC machining, or low-pressure casting methods. The downside is that these parts may be less durable, and the unit cost will be higher than mass-produced injection parts — but still much cheaper than covering the full mold cost over a small quantity.
-
Sheet metal enclosures are often a better option for small-batch products. They don’t require large mold investments, offer good structural strength, and are suitable for larger products. Although the unit cost of sheet metal parts is higher, it’s still more economical than amortizing injection mold costs over a small batch — especially when annual volumes are just dozens or hundreds of units.
-
Vacuum forming (thermoforming) is another process worth considering for low-volume designs, especially for large equipment housings where mold costs for injection molding would be astronomical.
Supplier resources are also critical. Different types of suppliers cater to different product strategies. For example, some injection molding factories that focus on household goods can offer cheap molds and low unit prices, but they require large order volumes to be viable. On the other hand, there are molders specializing in small-batch production — their molds are more expensive, and unit prices are higher, but their equipment and workflows are optimized for small orders.
Ultimately, successful product realization expresses the product’s technical features, functionality, component transitions, surface finishes, and color schemes — all contributing to its internal quality. A new product typically “starts with an idea and ends with mass production.” Every product is the result of teamwork, involving collaboration among professionals from different backgrounds and disciplines throughout the process.